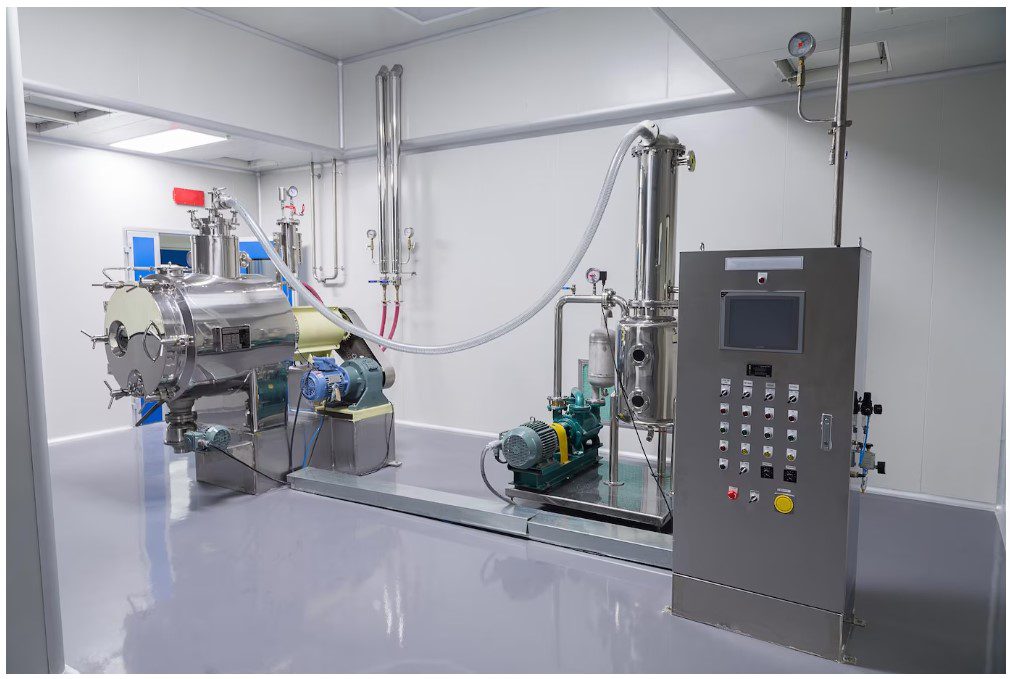
01 Jul The Ultimate Guide to Anti-Static Epoxy Flooring
Welcome to our comprehensive guide on anti-static epoxy flooring. In this article, we will delve into the world of anti-static epoxy flooring, exploring its benefits, applications, installation process, and maintenance. Whether you are a business owner, a facility manager, or someone interested in understanding this specialized flooring solution, we’ve got you covered.
What is Anti-Static Epoxy Flooring?
Anti-static epoxy flooring is a highly effective solution designed to control electrostatic discharge (ESD) in environments where static electricity can pose a threat to sensitive equipment, products, or personnel safety. This type of flooring is commonly used in industries such as electronics manufacturing, laboratories, cleanrooms, data centers, healthcare facilities, and more.
Benefits of Anti-Static Epoxy Flooring
1. Electrostatic Discharge Protection
The primary benefit of anti-static epoxy flooring is its ability to dissipate static electricity, preventing potentially damaging electrostatic discharges. By providing a conductive path for static charges to flow safely to the ground, this flooring minimizes the risk of equipment malfunction, data loss, and electrical shocks.
2. Safety and Personnel Protection
Anti-static epoxy flooring ensures the safety of personnel working in environments with sensitive electronic equipment. By eliminating static charges, it reduces the risk of accidental electrostatic discharges that could harm employees or damage critical systems.
3. Equipment and Product Protection
Sensitive electronic equipment and components can be easily damaged by static electricity. Anti-static epoxy flooring provides a protective barrier, safeguarding these items from electrostatic discharge, ensuring their longevity, and reducing the need for costly repairs or replacements.
4. Chemical and Abrasion Resistance
Anti-static epoxy flooring offers excellent resistance to chemicals, oils, solvents, and abrasions. This durability makes it suitable for a wide range of industries, including manufacturing, pharmaceuticals, automotive, and more, where spills, heavy machinery, or foot traffic may occur.
5. Hygienic and Easy to Clean
In environments that require high cleanliness standards, such as healthcare facilities and laboratories, anti-static epoxy flooring is an ideal choice. Its seamless, non-porous surface prevents the accumulation of dirt, dust, and bacteria, making it easy to clean and maintain a sterile environment.
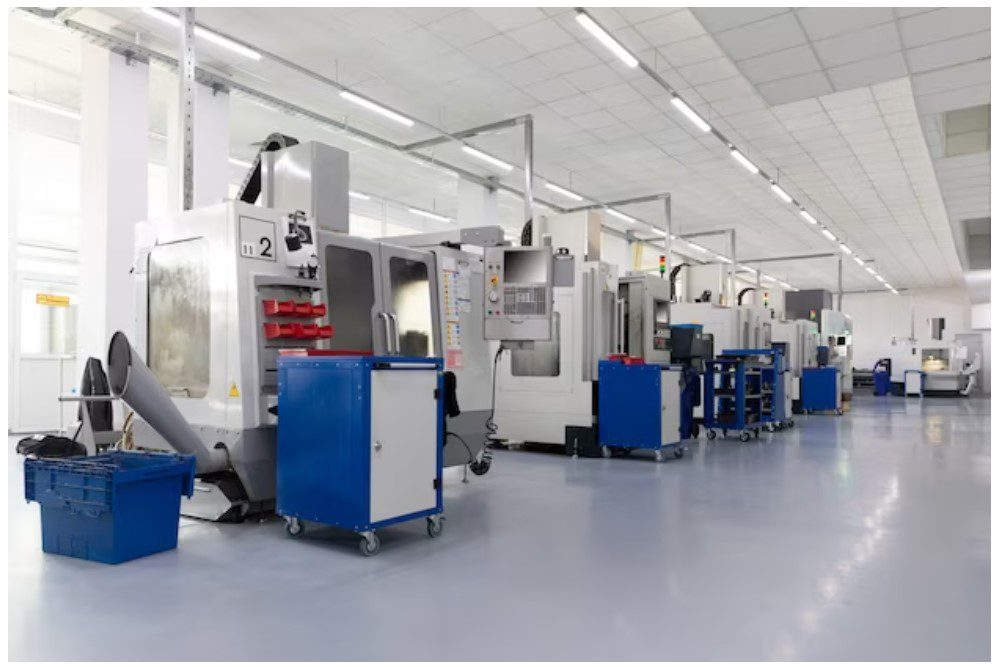
Applications of Anti-Static Epoxy Flooring
Anti-static epoxy flooring finds its applications in various industries and environments. Here are some of the key areas where this specialized flooring solution excels:
1. Electronics Manufacturing
Electronic components are extremely sensitive to static electricity, and even a small electrostatic discharge can cause irreparable damage. Anti-static epoxy flooring is widely used in electronic manufacturing facilities to create a static-free environment, protecting delicate components during production, assembly, and testing processes.
2. Laboratories and Cleanrooms
Laboratories, research facilities, and cleanrooms require precise control of static electricity to maintain the integrity of experiments, testing, and production. Anti-static epoxy flooring ensures a static-free environment, safeguarding delicate samples, instruments, and processes.
3. Data Centers
Data centers house critical IT infrastructure, including servers, networking equipment, and storage systems. Static electricity can disrupt data transmission and damage sensitive electronics. Anti-static epoxy flooring provides a static-safe environment, protecting valuable data and ensuring uninterrupted operations.
4. Healthcare Facilities
In healthcare settings, where electrostatic discharge can interfere with sensitive medical equipment, anti-static epoxy flooring is crucial. Operating rooms, laboratories, and diagnostic areas benefit from this flooring solution, as it minimizes the risk of static electricity compromising patient safety and the accuracy of medical procedures.
5. Manufacturing and Industrial Facilities
Manufacturing and industrial environments often involve heavy machinery, volatile substances, and high foot traffic. Anti-static epoxy flooring offers a durable, static-free surface that can withstand the demands of these industries while protecting personnel, equipment, and products.
Installation Process of Anti-Static Epoxy Flooring
Installing anti-static epoxy flooring requires expertise and precision. Here is an overview of the typical installation process:
- Surface Preparation: The existing floor is thoroughly cleaned, removing any contaminants or debris that could affect adhesion.
- Priming: A specialized primer is applied to enhance the bond between the substrate and the epoxy flooring system.
- Epoxy Application: The anti-static epoxy coating is applied in multiple layers, including a conductive layer, to ensure proper dissipation of static charges.
- Optional Topcoat: A topcoat may be applied to enhance the flooring’s durability, chemical resistance, and aesthetics.
- Curing: The flooring is left to cure for the recommended time, allowing it to achieve its full strength and performance characteristics.
- Quality Inspection: The installed flooring undergoes a thorough inspection to ensure it meets the required standards and specifications.
Maintenance of Anti-Static Epoxy Flooring
Proper maintenance is essential to maximize the lifespan and effectiveness of anti-static epoxy flooring. Here are some key maintenance practices:
- Regular Cleaning: Sweep or vacuum the floor regularly to remove dirt and debris. Follow up with damp mopping using a mild detergent solution.
- Prompt Spill Cleanup: Immediately clean up spills to prevent staining or damage to the flooring. Use a non-abrasive, pH-neutral cleaner suitable for epoxy surfaces.
- Avoid Harsh Chemicals: Harsh chemicals, such as acids or solvents, can degrade the epoxy coating. Use only recommended cleaning products to maintain the flooring’s integrity.
- Protect Against Heavy Loads: Use furniture pads, floor protectors, or other suitable methods to prevent heavy objects from scratching or indenting the surface.
- Regular Inspections: Conduct periodic inspections to identify any signs of wear, damage, or areas in need of repair. Address issues promptly to prevent further deterioration.
Conclusion
In conclusion, anti-static epoxy flooring is a versatile and essential solution for environments where static electricity can pose risks. Its ability to dissipate static charges, provide safety, protect equipment, and offer durability makes it a preferred choice across industries. By understanding its benefits, applications, installation process, and maintenance requirements, you can make informed decisions about implementing anti-static epoxy flooring in your facility.
- Comprehensive guide on anti-static epoxy flooring
- Benefits, applications, installation process, and maintenance
II. What is Anti-Static Epoxy Flooring?
- Definition and purpose of anti-static epoxy flooring
- Control of electrostatic discharge (ESD)
- Environments where static electricity can pose a threat
III. Benefits of Anti-Static Epoxy Flooring
- Electrostatic Discharge Protection
- Prevention of damaging electrostatic discharges
- Conductive path for static charges to flow to the ground
- Safety and Personnel Protection
- Reduction of accidental electrostatic discharges
- Ensuring the safety of personnel and critical systems
- Equipment and Product Protection
- Safeguarding sensitive electronic equipment
- Protection against electrostatic discharge damage
- Chemical and Abrasion Resistance
- Resistance to chemicals, oils, solvents, and abrasions
- Durability for various industries and environments
- Hygienic and Easy to Clean
- Non-porous, seamless surface for cleanliness
- Easy maintenance and sterile environment
IV. Applications of Anti-Static Epoxy Flooring
- Electronics Manufacturing
- Protection of delicate components during production
- Static-free environment in assembly and testing processes
- Laboratories and Cleanrooms
- Control of static electricity for precise experiments
- Safeguarding delicate samples and instruments
- Data Centers
- Protection of critical IT infrastructure
- Prevention of data disruption and damage
- Healthcare Facilities
- Interference prevention in medical equipment
- Ensuring patient safety and accurate procedures
- Manufacturing and Industrial Facilities
- Durable surface for heavy machinery and foot traffic
- Personnel, equipment, and product protection
V. Installation Process of Anti-Static Epoxy Flooring
- Surface Preparation
- Thorough cleaning and removal of contaminants
- Preparation for proper adhesion
- Priming
- Application of specialized primer for enhanced bond
- Substrate and epoxy flooring system compatibility
- Epoxy Application
- Layered application for proper static charge dissipation
- Conductive layer for effective functionality
- Optional Topcoat
- Enhancement of durability, chemical resistance, and aesthetics
- Additional protective layer
- Curing
- Recommended time for full strength and performance
- Achieving desired characteristics
- Quality Inspection
- Thorough inspection to meet standards and specifications
- Assurance of proper installation
VI. Maintenance of Anti-Static Epoxy Flooring
- Regular Cleaning
- Sweeping, vacuuming, and damp mopping
- Removal of dirt and debris
- Prompt Spill Cleanup
- Immediate action to prevent staining or damage
- Suitable cleaning products for epoxy surfaces
- Avoid Harsh Chemicals
- Protection against degradation of epoxy coating
- Use of recommended cleaning products
- Protect Against Heavy Loads
- Preventing scratches or indentations from heavy objects
- Use of suitable furniture pads or floor protectors
- Regular Inspections
- Periodic checks for wear, damage, or repairs
- Timely addressing of issues to prevent